+100K FRT GLOBAL CEMENT TRANSPORT
UTC Handles +100K frt Multimodal Cement Plant Delivery
UTC's Global Cement Division managed the transport of over 100,000 freight tons of equipment for one of the largest cement plants in the USA.
Multiple modalities were used for hundreds of shipments, some with pieces over 25', arriving from China, India, Germany, Italy, Romania, Turkey, Egypt, and Mexico.
With equipment heights over 25ft, the main transportation challenge was shipping major components in the largest configuration possible.
Planning began in 2019 with detailed route and feasibility studies, risk assessments, and evaluation of discharge ports.
Transporting equipment to the job site, located deep in the US Heartland, required intricate planning and creative solutions. To ensure all parties stayed informed in real-time, UTC created a customized portal for the client where information on the project was available. This enabled teams worldwide to address challenges and implement contingency plans quickly. Constant communication with a myriad of local authorities during last-mile transport, including utilities and cable companies, ensured the success of this complex project.
Out-of-gauge ocean freight to the Port of New Orleans via 12 charter vessels
The largest pieces originated in China, where they were barged to the Ports of Shanghai and Tianjin and loaded onto 12 charter vessels headed for the Port of New Orleans. Shipping the largest parts from China proved to be complex due to COVID lockdowns and unexpected last-minute restrictions. Port congestion, labor shortages, lack of raw materials, and quarantine requirements for cargo originating in active COVID regions posed challenges. UTC was able to call on existing relationships with carriers to secure space, contain vessel detention costs, and postpone shipment dates when cargo was not available for loading.
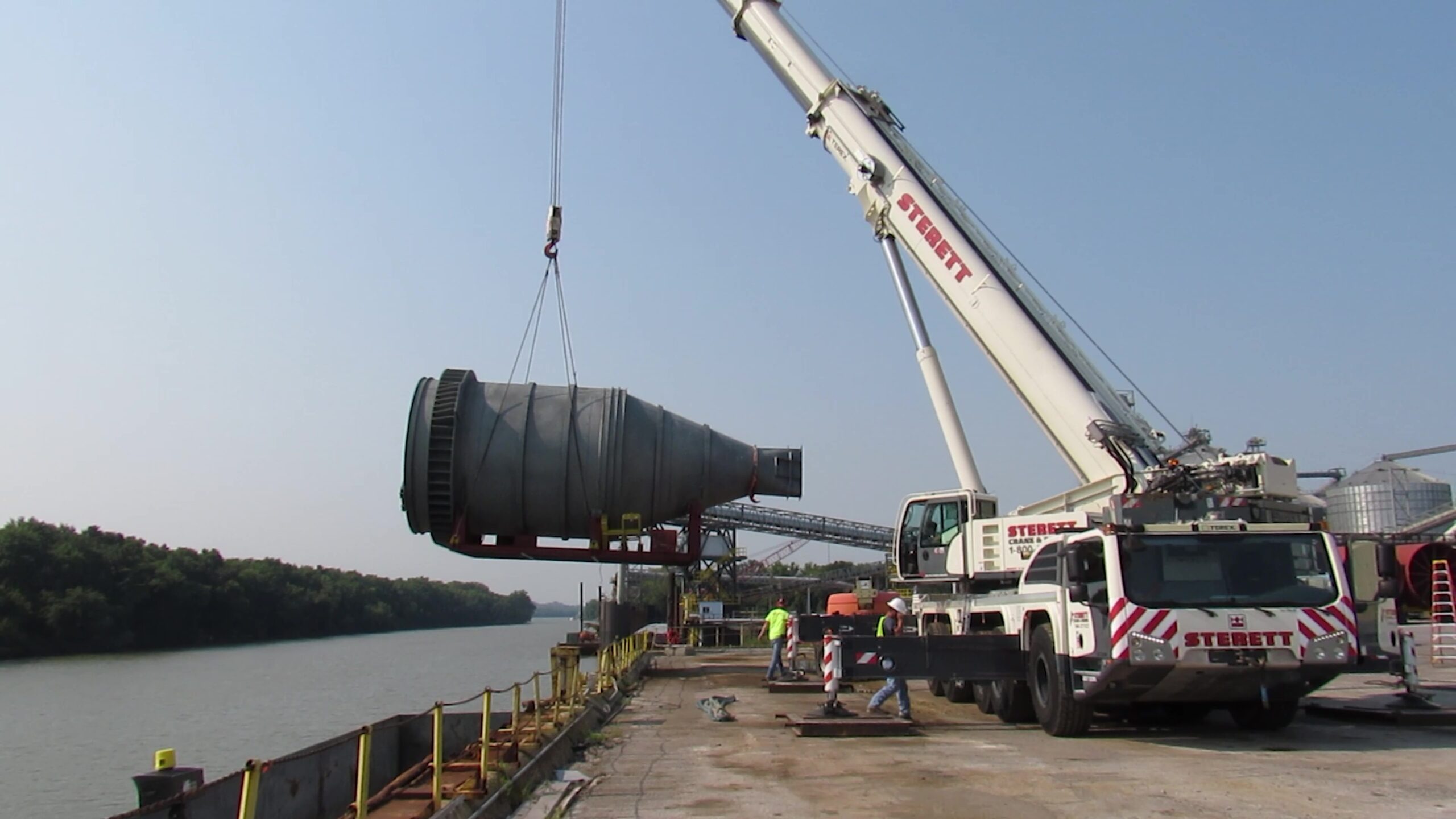
The next challenge: critical cargo urgently needed
Critical pieces of cargo became available in Chennai, India, in late 2021 and were urgently needed to meet the construction schedule. UTC’s team in India immediately began evaluating alternative options for time- and cost-effective transport, taking into account extremely tight capacity and heavy monsoon rains. UTC determined the best strategy would be to truck the equipment to Mumbai, where it would be loaded onto four ro-ro vessels.
Other major OOG cargo originated in Romania, Italy, Turkey, and Germany and were shipped to the US via breakbulk vessels, with some smaller parts and accessories shipped via airfreight. Additional parts and accessories out of Mexico were transported overland via 150 truckloads to the site in Mitchell. UTC handled customs at the border.
Barge transport up the Mississippi River
Once the oversized cargo was discharged in the US, it was loaded onto 37 chartered hopper barges for transport to the Port of Jeffersonville. UTC scouted multiple locations to determine the final destination port, considering supply chain delays, port congestion, adverse weather events, and more. Port of Jeffersonville was chosen because of its proximity to the job site and ease of entering highways with oversized equipment.
Deliveries of large-scale projects like this are usually carefully sequenced so equipment and parts arrive in the order they are installed. However, with COVID lockdowns, supplier delays, and shipping backlogs causing significant uncertainty in production and delivery schedules, UTC took delivery of parts as soon as they were available, storing them at the port until needed at the plant.
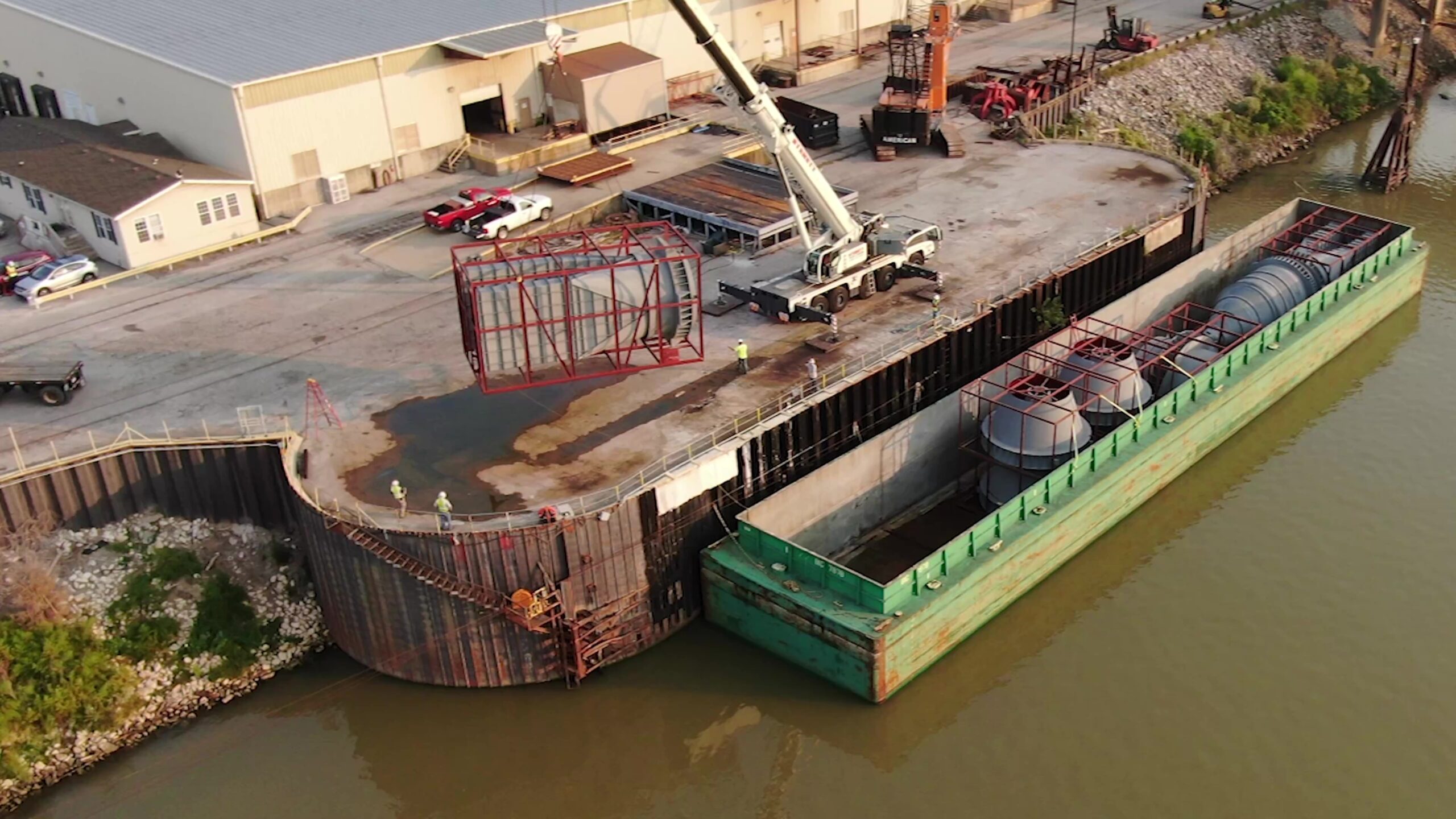
Last-mile delivery: Interfacing with local utilities, DOT, & wildlife authorities
UTC consulted with local utilities, DOT, and wildlife authorities to ensure the last-mile transport of hundreds of oversized pieces spanning 24 months would not interfere with the local community and surrounding habitats.
Before transporting any equipment, UTC engaged with Indiana DOT (INDOT) to analyze last-mile route options.
Once a 71.7-mile route was established, UTC entered into a $4M bond with INDOT, allowing site revisions and travel route modifications to accommodate oversized cargo. UTC representatives and DOT contractors traveled the entire route, measuring and identifying all communications and electric lines and overhanging obstacles. Working with additional contractors, utility wires and poles, traffic lights, highway signs, and digital messaging boards were temporarily lifted or removed during transports. Most larger utilities authorized Kenco to raise their wires, but several REMCs required their engineers to be on-site to ensure the safety of their lines. Several major telecoms and electric cables leading up to Chicago were along the route, meaning utmost care had to be taken to avoid widespread disruptions. With careful planning and precise attention to detail, all oversized pieces of equipment were moved without incident.
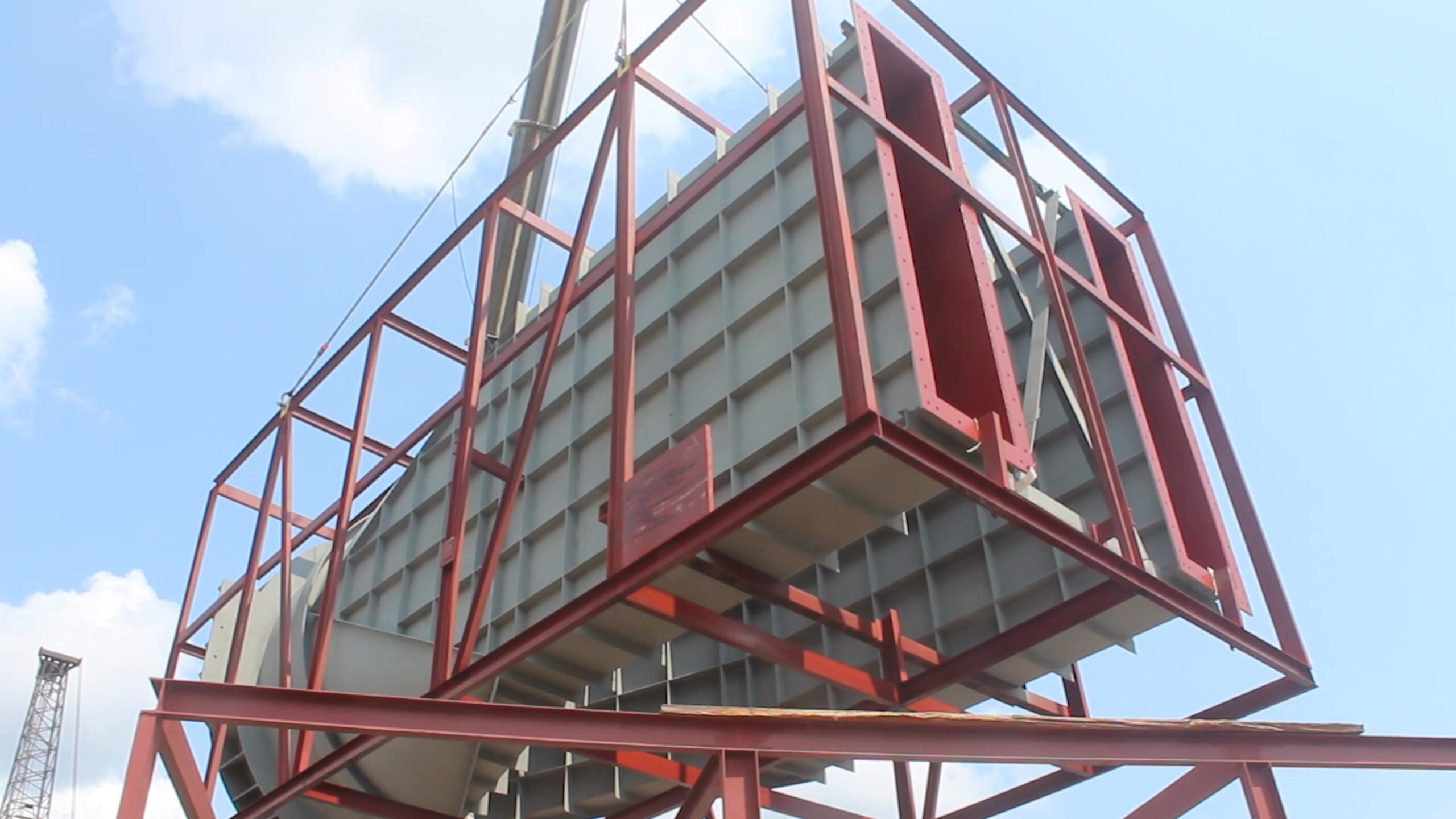
INDOT required that any cargo over 18’ tall must be transported overnight.
The largest pieces came in steel crating to facilitate loading and provide protection. However, the crating made round, tapered pieces into otherwise square cargo, which would need significantly more overhead clearance. By cutting and removing top portions of the crating, several pieces were transported without stretching utility lines or removing overhanging obstacles. These were trucked using specialized perimetral trailers, which provided additional height clearance due to their very low base. They moved in convoys of 2-3 loads to further minimize movement of utility lines and obstacles. Multiple packages were so wide, the roads so narrow, and the placement of telephone poles close to the street that there were just inches of clearance at certain times.
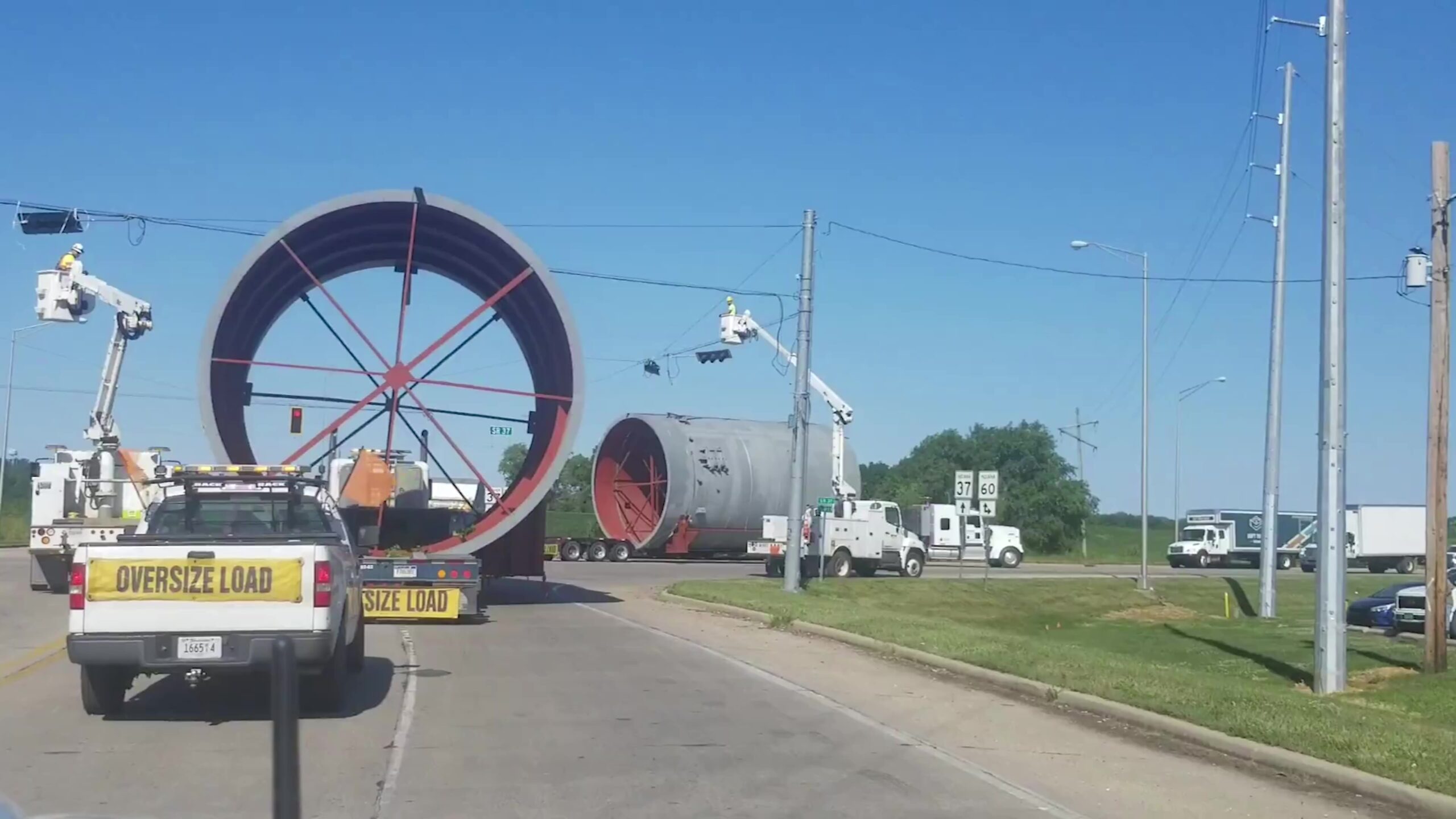
Last-mile transportation of these oversized pieces endured the depths of winter through ice storms and snow, through spring rains, and into the hot summer, or bat season.
Since the Indiana bat is an endangered species and an integral part of the local ecosystem, UTC interfaced with local wildlife authorities to ensure that continuous overnight transports of oversized equipment would not disrupt the population, which make their home in the hardwood trees lining the route.
UTC’s strength is adapting to the client’s needs, which changed as the project progressed. The pandemic, lockdowns, port closures, reduced labor pools, escalating shipping costs, and vessel availability were all contributing factors. Contingency planning for these types of disruptions is fundamental in executing a project of this magnitude. Fortunately for UTC’s Cement Division, their skill, years of experience, and advanced planning allowed the freight to move uninterrupted. The job was well-executed, safely, and on time.
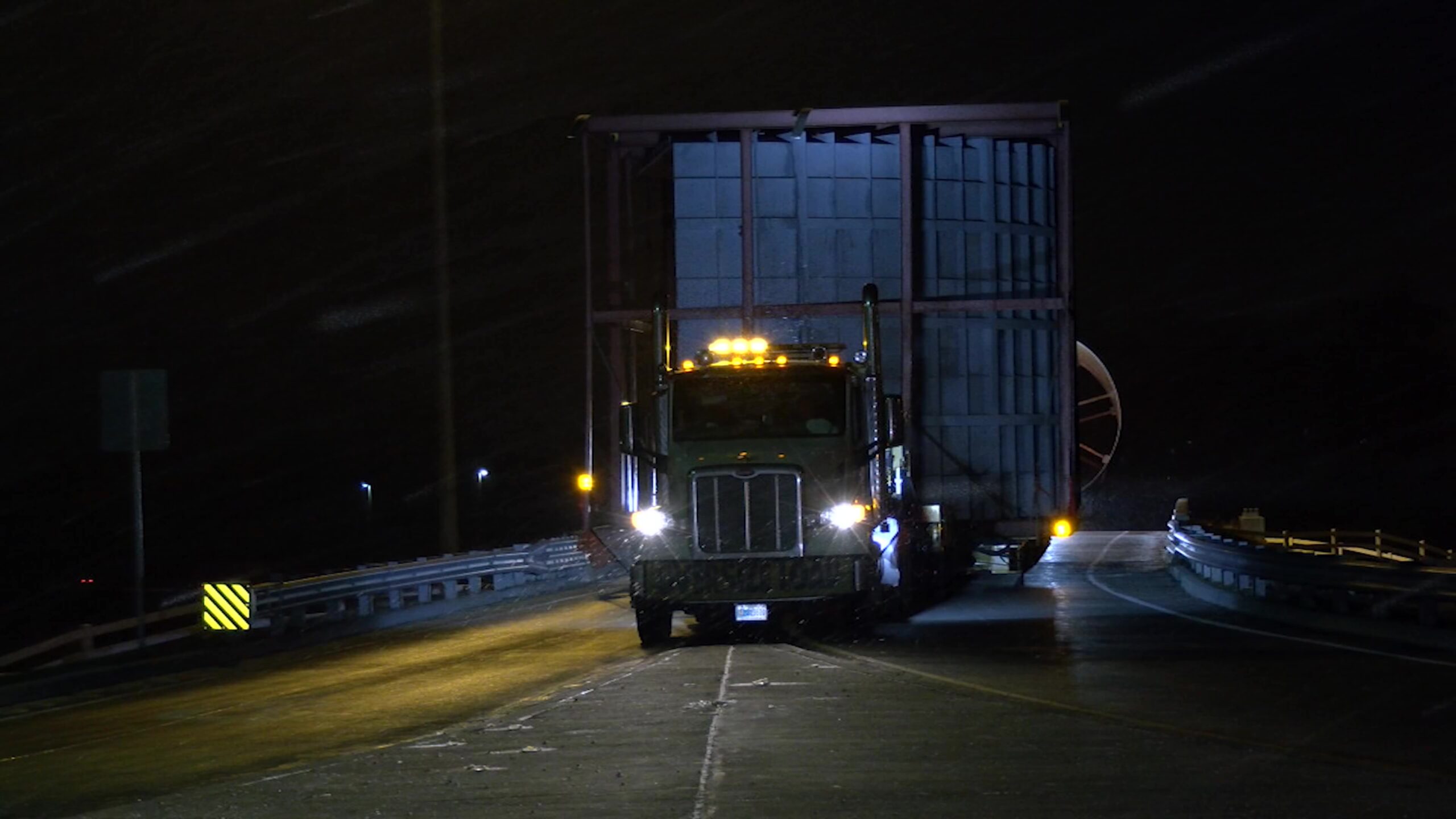