High-Tech high stakes greenfield cement plant transportation
high-tech cement
UTC Overseas was contracted to move a cement plant for the Elementia Group, managing cargo from various European countries and shipping to the Yucatan region in Mexico.
A new greenfield plant was to be constructed and UTC's cement team had the experience and knowledge to coordinate all facets of this challenging delivery.
Cement has been around since Roman times, but the way it is made has changed radically, with advancements in manufacturing made every year. Processes have gone high-tech, and equipment has become more sophisticated. Transporting this state-of-the-art, high ticket machinery and related supplies requires great precision and skill to ensure proper handling and safe delivery. This is where UTC Overseas comes into the equation.
UTC's high-tech cement experts consulted with our client to design modular cement equipment to minimize transportation costs.
This massive job did not just involve moving cargo from point A to point B; it required expertise in transport modalities, port specifications, machinery knowledge, international and regional regulations, and IT solutions for 24/7 communications and shipment tracking. UTC's team of professionals had the logistics and technical knowledge, as well as personnel and capital resources to manage this large-scale door-to-door project destined for a complex and hard-to-reach part of the world.
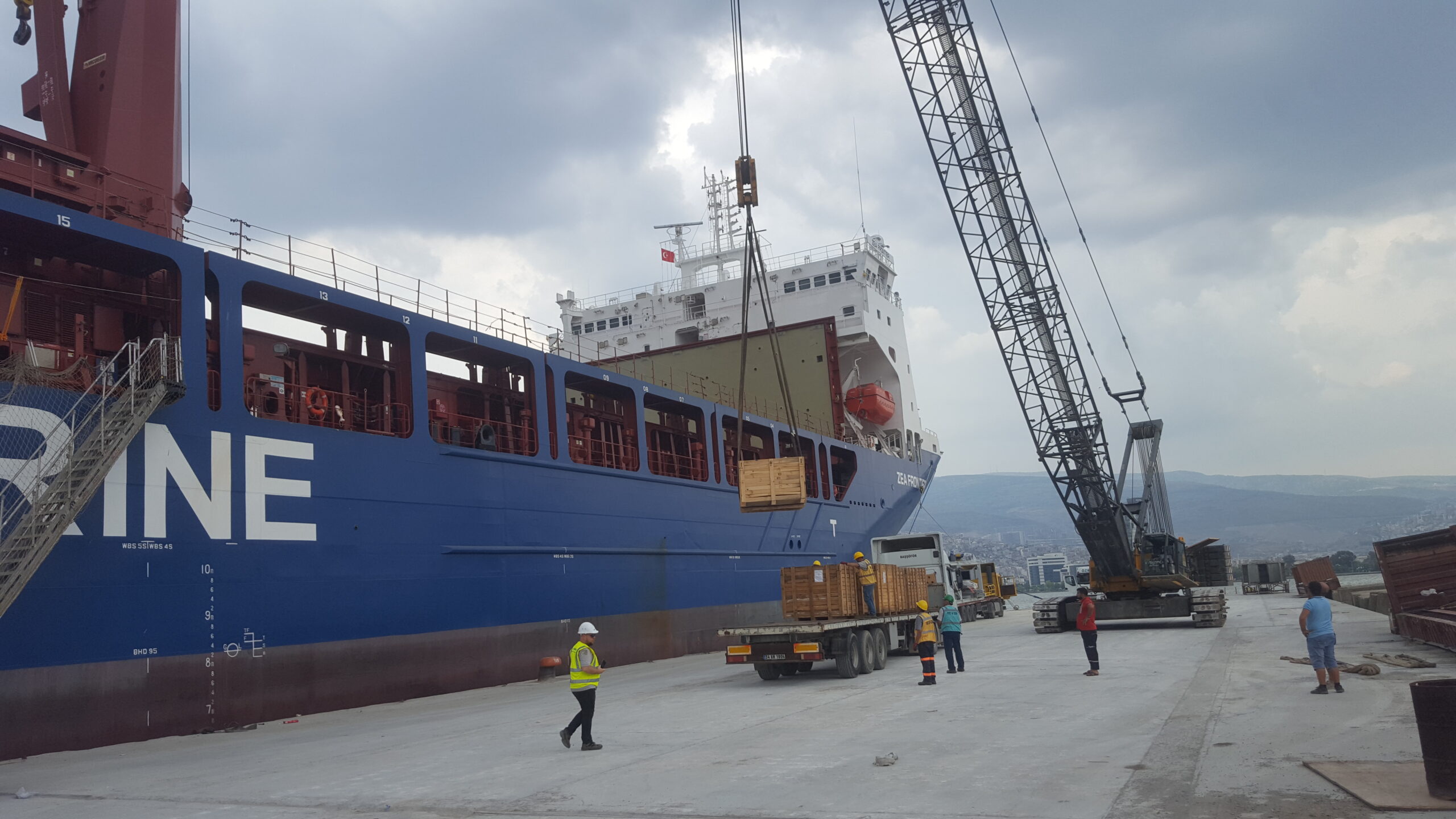
UTC began planning in 2019, and the process continued for an entire year. Early on, the client involved UTC to optimize equipment designs to ensure efficient and cost-effective transport. Jointly, they agreed that pieces would be knocked down, shipped unconstructed, and assembled at the site. UTC evaluated the pieces for size, weight, and mass, suggesting the most reliable ways to lift, load, and transport.
When COVID hit, UTC's knowledge of international and local regulations and attention to safety ensured cargo kept moving.
In early 2020, amid the Covid pandemic, the freight began to move. Equipment and supplies from Germany, Italy, Spain, and Turkey were loaded at several European ports and were destined for the port of Progreso, primarily a passenger cruise destination. From start to finish, the project spanned 14 months. The port infrastructure was vetted, and route surveys were done to ensure a safe and reliable route to the plant. Clearing assets along the way with local authorities was critical, and necessary personnel were in place to lift signs, signals, cables, and lines. Safety measures were of the utmost importance, and Covid protocols required adjustments with short notice.
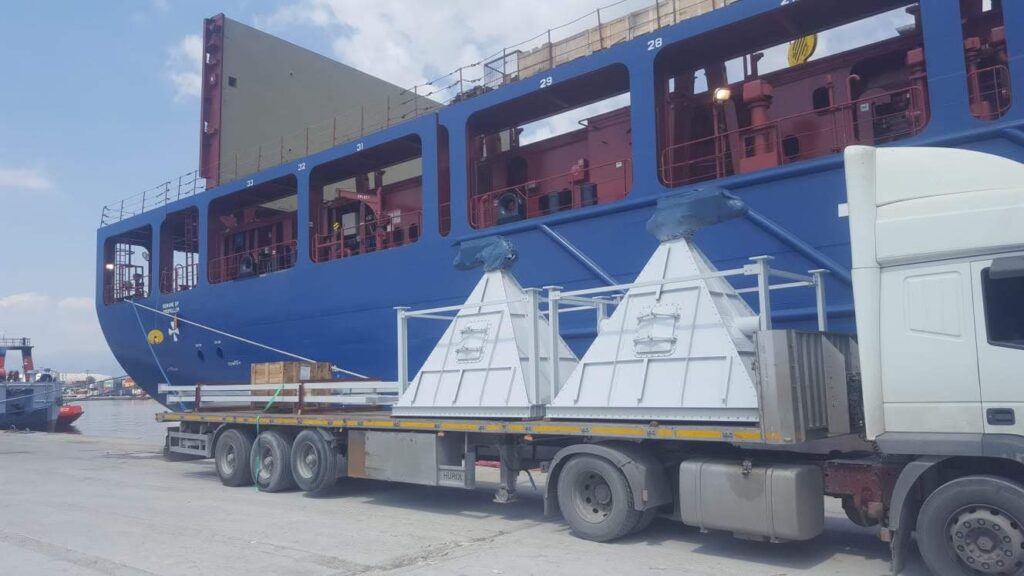
With a project of this magnitude, communication and keeping all stakeholders informed was critical to the successful execution. UTC's business model and SOP's outline consistent practices that include constant monitoring and regular updates that translate into value for the customer. UTC created a dedicated client portal to allow all project participants to access up-to-the-minute shipping information, documentation, milestones, and KPI's 24/7, whether they are in an office, in the field, or on the job site. This kept all partners fully informed at all times.
UTC's global network worked hand-in-hand to coordinate 3500+ pieces of equipment sourced from four countries.
UTC's team handled ocean and inland transportation for the complete door-to-door move of the oversize, overweight pieces. In total, there were over 3500 pieces and more than 800 trucks. Constant communication between UTC's Mexico, US, Turkey, Germany, and Italy offices along with the client, port, vendors, and plant was critical to ensuring a smooth operation. UTC professionals had the ability to mobilize vendors and adapt to the changing needs that arose.
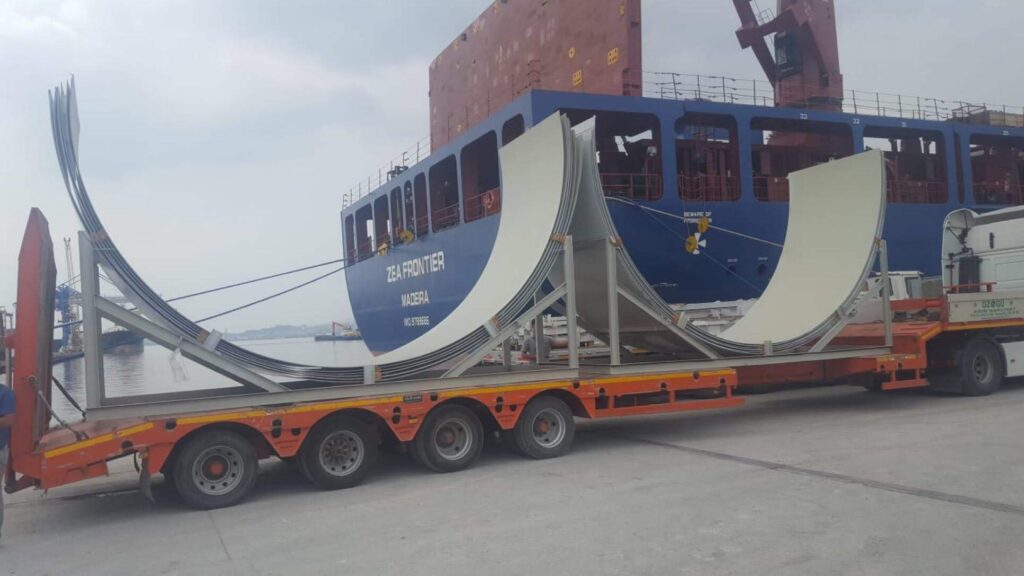
What does this mean for the Yucatan Region? In an area that needed an infusion of capital investment to boost the economy, 450 new jobs were created. The Progreso plant is the first production facility in the area, and operations commenced in September 2020. Sustainability was a factor, and with efficient use of electrical power and water consumption, the plant will have a minimum impact on the environment. It is a win-win for the area.
As the architect of this massive plan, Vice President Projects and Head of UTC Cement Division Rodrigo Chittoni comments, "Global trade today is facing tremendous challenges, and flexibility is key as plans made today may need to change tomorrow. A massive cement plant move requires that all aspects be reviewed daily and adjusted due to Covid, weather, and other circumstances. Constant monitoring and astute attention to detail are paramount to successful delivery. Fortunately, this is how UTC operates, and the client benefits from UTC's extensive knowledge in cement logistics and our years of experience in this specialized market. The outcome for the Progreso plant was a successful delivery – on time, within budget, with all equipment safely delivered."